
Speak to our technical team about pail filling:
sales@paquip.com or call/text (813) 252-0206
Request a Quote for Additional Options:
- Stainless steel / Washdown - for food processing applications
- Diving nozzles - for foam control, reducing splashing, or controlling fuming
- Full automation - including powered conveyor, label applicator, lid placement, and lid press
- Additional nozzle types - such as for paints/coatings, food processing, or viscous fluids
- Additional conveyor options - tighter roller spacing, washdown, powered systems, custom heights/lengths, curved sections, and transfers
- High accuracy scales - Resolution down to 0.02lb and repeatability down to +/-0.05lb
- Container positioners - for jerrycans/carboys, bag-in-box, or smaller bottles, such as 1 gallon
- Nozzle & hose quick-change systems to limit contamination between production runs
- Corrosive products - all plastic wetted systems available
- Hazardous locations - Class I Division 1 or 2
- Nitrogen blanketing
- Splash guard
- Compressed air/nitrogen clearing - Assists removing residual fluid
- Additional pump options
- Additional power options (120v to 575v)
- CIP suitable systems
- Mobile casters
The XPG-200 is a dual nozzle, semi-automatic pail filling machine designed with two pumps for viscous as well as easy-flowing product. Separate plumbing systems allow for high speed filling of two pails at a time or for separation of different fluids. The XPG-200 is a dual nozzle/pump version of the XPG-100.
Increase your pail filling capacity or blend two different fluids directly in the pail using a dual pump system. Options are available for filling containers as small as 1 gallon.
Packages available specifically for your industry:
Coatings (paint, epoxy, urethane) Lubricants Agricultural Personal Care Food-processing Chemicals Cleaning Products Adhesives
Additional Information:
Pail filling process
with mixing of fluids and lid closing
Standard equipment includes: Fixed nozzle, pump, scale, and powder coated frame. Diving nozzle, washdown, and hazardous location packages are available.
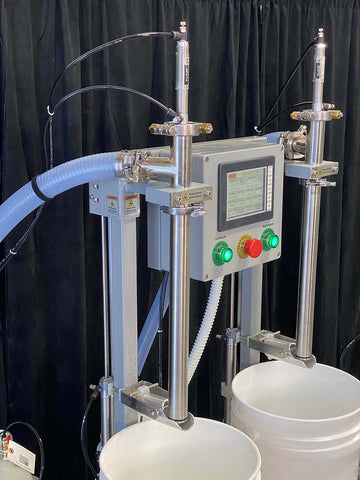
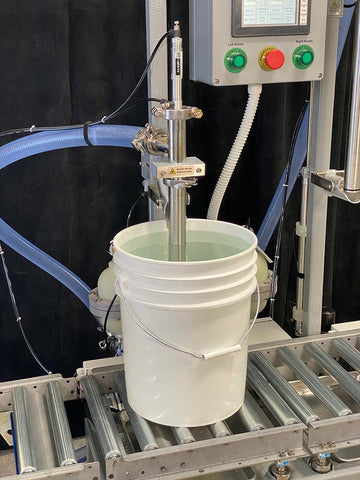
Pail filling capabilities, included standard:
- Independent 16.5”x15” roller conveyors with load cells
-
Fast filling speeds:
- Gear pump: up to 15 seconds (for two 5 gallon pails)
- Centrifugal pump: up to 9 seconds (for two 5 gallon pails)
- Air-operated pump: up to 9 seconds (for two 5 gallon pails)
- Fill all types of pails: open top, square carboys, etc
- Fill liter, quart, or gallon containers (requires additional options)
- 7” touch screen for weight readout, setting weight target, and motor speeds
- Save up to 255 fill profiles for different container sizes and products.
- Integrated quality checklist via the touch screen for switching between fill profiles and during system startup. (available option: barcode or RFID scanner integration for verifying supply tank, pump, or nozzle matches selected fill profile)
- Variable fill speed with auto slow top off feature
- Up to 1.5” hoses available to accommodate higher viscosity fluids
- Adjustable height no-drip nozzle
- Sanitary fitting connections for easy hose swaps
- Advanced computer controls with out-of-fluid detection, nozzle open detection, unexpected weight on scale, air-supply pressure monitoring, and more
Standard filling machine equipped with:
- (2) pumps, independently operated with optional materials and seals for fluid compatibility
- 7" Color touch screen
- Roller conveyor scales
- Powder coated welded steel frame (stainless steel washdown or epoxy coated corrosion resistant frame available)
-
Sanitary/tri-clamp stainless steel wetted path with 1.5" supply hose barb connection. Pump wetted materials may vary.
- Fully adjustable nozzle position - Adjust the nozzles up and down to fit any pail type up to 18” high (additional height available upon request)
Filling Specifications:
Fill Speed | Up to 12 CPM |
Measurement Method | Weight¹ |
Fill Accuracy | +/- 0.1 lb (gear pump) +/- 0.2 lb (centrifugal pump) +/- 0.2 lb (AODD pump) (high-accuracy models available) |
Viscosity Range | 1-10,000 cP (gear pump) 1-800 cP (centrifugal pump) 1-50,000 cP (AODD pump) 1-1,000,000 cP (rotary lobe pump) |
Fluid Particulates | Yes, depending on pump type |
Fluid Temperature | Max: 120°F (49°C) Min: 32°F (0°C) (additional temp range available) |
Fluid Supply Requirements |
Gear, lobe, & Air-operated pumps: self-priming pumps can draw fluids from ground-level (such as from an IBC tote) Centrifugal pumps: requires elevated fluid source or a vacuum primer to initially fill pump housing. |
Corrosive Fluids | Yes, depending on pump type (Plastic/non-metallic options and chemical-resistant epoxy frame coating available for highly corrosive applications.) |
Foamy Fluids | Yes |
Electrical Requirements | 240VAC 50/60hz, single phase, 35A for electric pump models 120VAC 50/60hz, 5A for air-operated pump models (Three phase and higher voltage available) |
Air Requirements | 80 PSI @ 5 CFM |
* Fill speed may vary based on fluid & bottle characteristics
* Optional parts and upgrades may be required for compatibility with certain fluids
¹ With standard equipment, the net weight measurement is used as a proxy for determining filled volume and not for legal-for-trade weight measurements. Contact Paquip if your application requires NTEP-certified scale equipment.
Optional upgrades:
- Various pump, nozzle, & hose options - customizable to suit your application and container size/dimensions
-
Pneumatic lid press - conveyor mounted with dual hand safety control
-
Stainless steel frame & scale - upgrade the scale assembly to stainless steel
- Explosive & Flammable Environments - Options for Class 1 Division 1 and Class 1 Division 2 available
- Compressed air line clearing - Helps clear residual fluid from the plumbing to aid in product changeovers.
-
Roller conveyor systems - expand your production capacity by adding roller conveyor to your filling system. Various roller spacing, diameters, and materials available.
-
Dye & chemical dosing - single and multiple dosing pump options
- Nitrogen dispensing - dispense nitrogen into pails during filling or via a separate station next to the XPG pail filler.
- Container-specific hardware - positioners for closed-head pails, bag-in-box neck positioners, splash guards, and other accessories available.